Module Framework
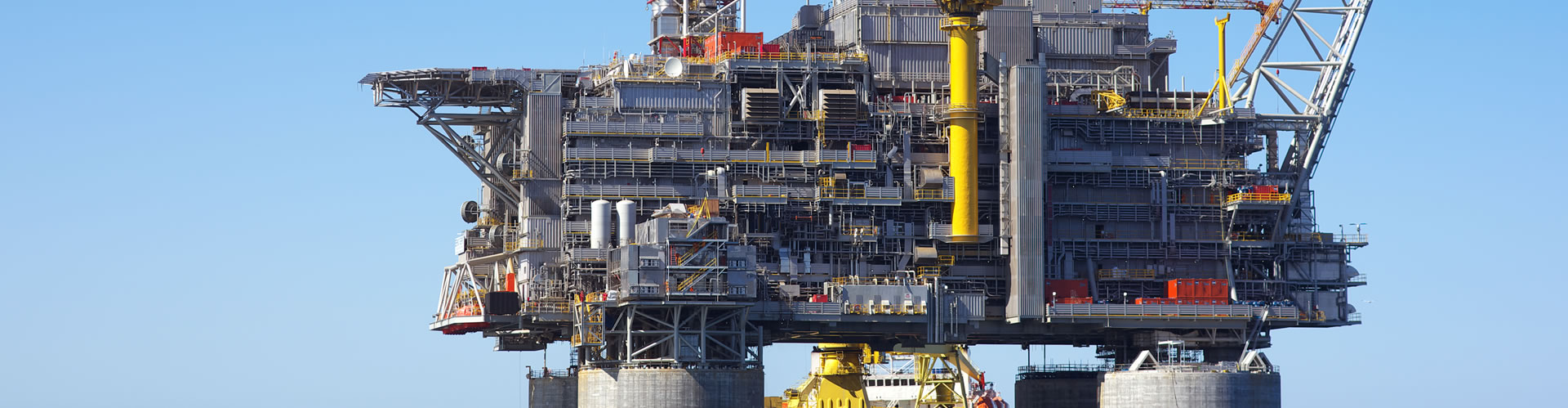
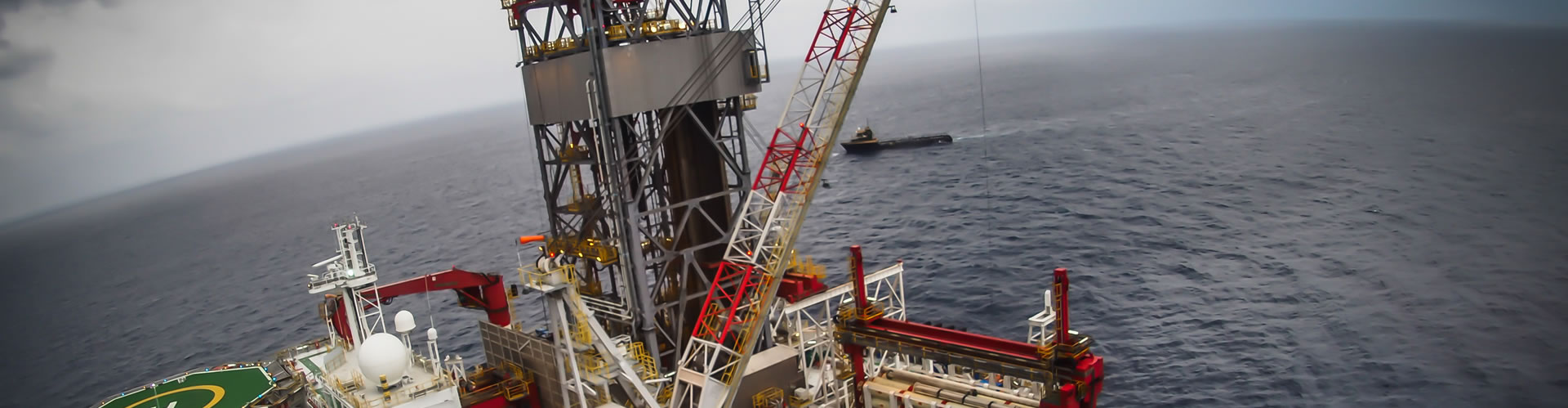
ONE is a modular framework focused on components, offering a variety of asset integrity management tools.
Clients can tailor ONE to fit their unique workflows, processes, and terminology, configuring it as a flexible toolkit for managing integrity data.
ONE Modules
ONE’s centralised repository standardises data input and output, enhances data retrieval and management, and simplifies expansion and updates with minimal effort. ONE’s standardised baseline significantly improves transparency and efficiency across all operational levels.
ONE manages tasks and issues for all equipment types, including Pipework, Pipelines, Vessels, Tanks, Heat Exchangers, and Rotating mechanicals.